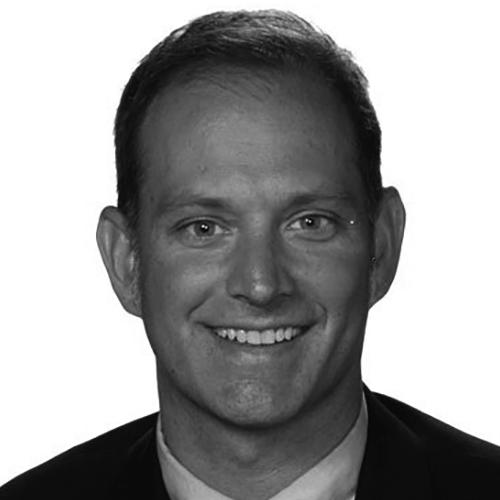
Mike Mikula
Chief Engineer, Ford Advanced Manufacturing Center
How is additive manufacturing/3D printing revolutionizing the factory of the future?
First, additive manufacturing allows tooling designs that are not possible using conventional technologies. This helps us reduce the cost, delivery time, and complexity, while improving the ergonomics of hand assembly tools, fixtures, and jigs.
Secondly, additive manufacturing will be used to reduce captive, in-plant inventories of spare parts (details that wear out) by converting to a strategy of “print on-demand.”
Lastly, additive manufacturing will enable localized manufacturing of our products where end-use parts can be printed where and when they are needed.
What barriers are keeping manufacturers from adopting the newest industrial technologies?
For additive manufacturing, the challenges remain in the areas of the maximum build size, speed, and accuracy of the printing process, but the rate of improvements across all additive technologies suggest this is a challenge the industry is rising up to overcome. The rate of general technology adoption is typically governed by the delicate balance between tactical value of solutions and the strategic significance of the solutions at scale. Often the enablers to protect scalability result in incremental effort and cost for initial adoption based on the need for the solution to be backwards compatible to legacy infrastructures.
What is one common misconception about Industry 4.0 technology you’d like to debunk for our readers?
That this is something new. Connected processes have existed, albeit at a primitive depth, for many decades and, as a result, there is a lot of knowledge and experience around where the unlocked potential value remains.
What advice would you give to manufacturers looking to create their own “futuristic factory?” Is there anything specific that you think creates a more profound impact?
Sometimes you need to “go slow to go fast.” You should take the time to really understand your current operation, and not just the factory, but all the interdependencies with things like product design, sourcing of parts, logistics, etc. Optimizing only a portion of the enterprise, like the factory, only provides a limited benefit and can inadvertently create a barrier to true Industry 4.0 realization if it isn’t thought through.
Where is Industry 4.0 headed next? What do you envision for the next 5-10 years of manufacturing?
The “next big thing” within the suite of what is Industry 4.0 is likely around artificial intelligence (AI) — not only the robustness of the AI engines, but also the strategy around where and when to leverage AI.
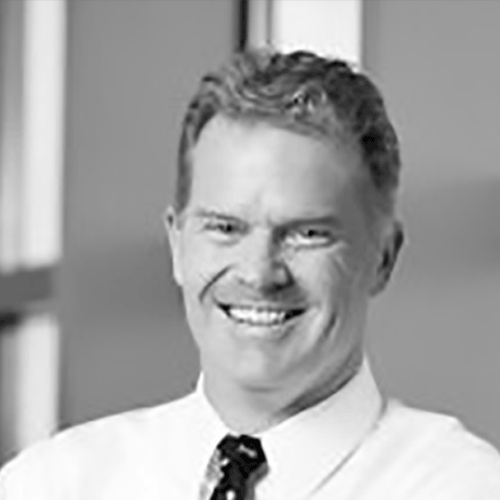
Peter Evans
Chief Digital and Marketing Officer, Optiv
What is one thing all businesses should incorporate into their Industry 4.0 strategy?
Get cybersecurity right first, as opposed to in response to Industry 4.0 initiatives. The rapid pace of digital transformation can drive business forward faster than security can keep up. As operations evolve and attack surfaces expand, a fully integrated and aligned cybersecurity strategy is essential to protecting the volumes of data, business IP, insights, and competitive advantages being generated by the automation of manufacturing operations.
What is the biggest mistake companies make when it comes to picking a cybersecurity vendor?
By selecting non-integrated cybersecurity technologies, in response to Industry 4.0 projects, organizations often fail to take advantage of existing security investments that could scale to address new cybersecurity concerns, fail to integrate for optimized security program efficacy, trigger unnecessary complexity and operational costs, or inadvertently create gaps in security coverage.
What barriers are keeping manufacturers from adopting the newest industrial technologies?
Talent shortages, expanding attack surfaces, non-integrated cybersecurity tools, and more breaches are all symptoms, and the challenges of an unnecessarily complex cybersecurity environment. These challenges are addressable by taking a broader view and designing fully integrated cybersecurity solutions that strategically optimize security tools, data, programs, and operations.
Can you provide a few examples of forward-thinking technologies in Industry 4.0 helping companies innovate their operations?
Smart, integrated cybersecurity systems that evolve as they get access to more data will help cybersecurity become more efficient, effective, and less complex. Ultimately, a network of digitally connected solutions that creates and shares information will leverage that same innovation to result in more powerful cyber protection, mirroring Industry 4.0 values.
Staff, [email protected]