Our panel of experts discusses how manufacturing empowers young professionals with rapid advancement, hands-on innovation, and long-term career security.
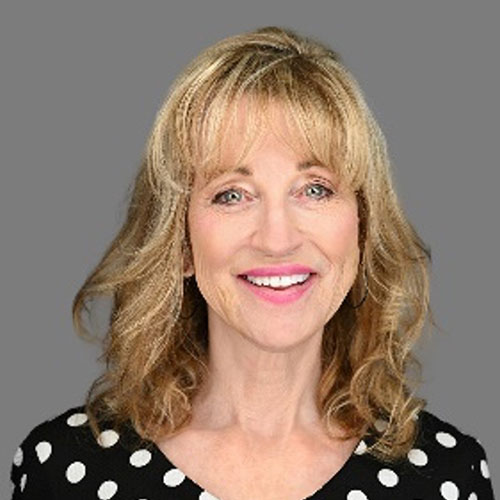
Kim Humphrey
CEO and President, Association for Manufacturing Excellence (AME)
What can young people expect in terms of professional growth when they pursue a career in manufacturing?
Manufacturing offers an exciting and vibrant career filled with meaningful opportunities for young professionals. It provides a clear pathway to advancement, competitive wages, and the chance to work in high-tech environments. Young people entering manufacturing can expect purpose-driven work with real-world impact. From producing essential goods to driving innovation, every role contributes to society in a tangible way.
Career progression in manufacturing is fast-paced. Employees can move into leadership roles within just 3 to 7 years, depending on individual performance and training. According to the U.S. Bureau of Labor Statistics, 60% of manufacturing employees are promoted within their first five years, thanks to ongoing skill development and employer investment in training. Starting salaries for skilled roles typically exceed $50,000. With experience and leadership growth, professionals can earn $100,000 or more in roles like engineers and plant supervisors.
Professionals in this field gain highly marketable technical, digital, leadership, and analytical skills that are valued not only in manufacturing but across many industries. Even more exciting is the access to cutting-edge technologies. Young people gain early, hands-on experience with AI, robotics, 3D printing, IoT, and digital twin technologies, positioning them at the forefront of industry innovation.
Manufacturing isn’t just a job; it is a fast-moving, future-ready career with purpose, impact, and exceptional growth potential. Manufacturing is here to stay, and by integrating technology, lean, and problem-solving techniques, there are unlimited opportunities for young people who want to join the journey.
What are some of the key reasons someone should consider a career in manufacturing?
By 2030, the United States is expected to have 3.8 million open manufacturing jobs, with over 2.1 million potentially unfilled due to a growing skills gap. This shortage makes manufacturing one of the most secure and in-demand career paths in today’s economy.
Compensation and benefits in manufacturing are also a major draw. The average annual compensation is $102,629, including wages, bonuses, healthcare, and retirement, significantly higher than the national private sector average.
Unlike many traditional careers, manufacturing often doesn’t require a four-year degree. Many roles start through apprenticeships, technical training, or certifications, allowing young people to earn while they learn and avoid student debt. This new model of skilled employment is creating a wave of so-called “new collar” workers. These are highly trained, tech-savvy professionals building strong careers without a college degree.
Innovation is at the core of modern manufacturing. Workers engage with cutting-edge technologies like robotics, artificial intelligence, data analytics, 3D printing, advanced materials, and smart factories. Far from outdated assembly lines, these are high-tech, future-focused work environments.
Manufacturing is also a global industry, offering opportunities for travel, relocation, and collaboration with international teams. It’s an ideal pathway for ambitious professionals looking to build versatile, world-ready careers.
How can manufacturers meet the needs of both seasoned professionals and next-gen talent?
To strengthen workforce continuity and engagement, manufacturers can implement mentorship programs that pair seasoned professionals with younger employees in formal, purpose-driven mentorship relationships. These programs promote knowledge transfer, build trust, and accelerate skill development across generations.
Fostering an inclusive, multi-generational culture is essential. Seasoned employees can mentor younger workers on craftsmanship and leadership, while next-generation employees can serve as reverse mentors, sharing insights on innovation, digital tools, and emerging technologies. This reciprocal model encourages mutual respect and continuous learning.
To support work-life balance and cross-functional collaboration, manufacturers can adopt flexible work arrangements, including adjustable shift schedules, task rotation, and collaborative problem-solving teams. Integrating advanced technology and automated systems also helps streamline workflows and increase efficiency across all career stages.
Research underscores the importance of meaningful work environments. Studies show that younger employees seek purpose and impact, while seasoned professionals value legacy and mentorship. According to Gallup (2023), purpose-driven workplaces are 54% more likely to retain both early- and late-career employees.
By creating people-centered leadership, embracing generational diversity, and investing in continuous development, manufacturers can build a resilient, future-ready workforce.
Where will manufacturing be 10 years from now?
Smart factories will become the norm. Manufacturing is evolving beyond automation toward intelligent autonomy, driven by technologies like AI-powered predictive analytics, digital twins, Industrial IoT (IIoT), edge computing, and 5G. These innovations will enable real-time decision-making, self-optimizing systems, and significantly reduced downtime.
However, the industry faces a projected shortfall of 2.1 million workers unless workforce development efforts accelerate. There will be a growing emphasis on upskilling, particularly in roles that require close collaboration between humans and AI.
Factories will also operate under stricter Environmental, Social, and Governance (ESG) standards, with production becoming increasingly localized. As a result, manufacturing will demand highly skilled professionals in STEM-focused roles, especially in clean energy and climate-resilient production.
This marks an exciting era for the manufacturing sector, with rapid innovation and transformation on the horizon.
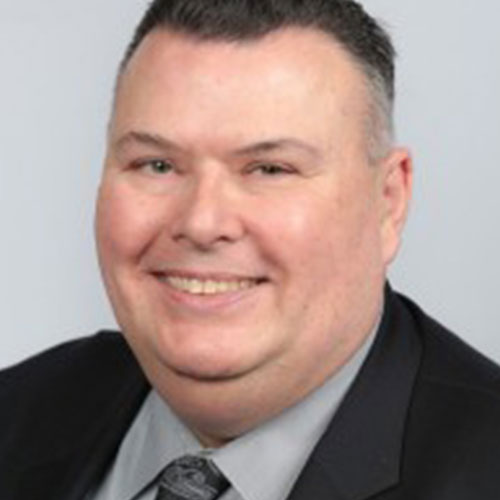
John P. Busel
Vice President, Composites Growth Initiative, American Composites Manufacturers Association (ACMA)
What can young people expect in terms of professional growth when they pursue a career in manufacturing?
When I first started out, the idea of climbing the ladder in manufacturing felt straightforward: Work hard, learn the ropes, and you’ll go far. That’s still true today, but now there are even more ways to grow. This industry offers so much more than production line work. I’ve worked alongside professionals in robotics, engineering, quality assurance, design, and management, and I’ve watched young workers rise quickly when they’re motivated and curious.
Manufacturing also puts a huge focus on skill-building. Programs like AMTEP, which offer free training and industry-recognized certifications, didn’t exist when I was starting out. Today, young professionals can train in CNC machining, automation, data analytics, and other high-demand areas. Apprenticeships are common, and they’re a great way to earn while you learn and build a career from the ground up.
What are some of the key reasons someone should consider a career in manufacturing?
From day one, I’ve loved that my work in manufacturing actually makes something — something real, useful, and lasting. That sense of purpose has kept me going for over 40 years, and it’s something I know many younger workers are looking for.
Today’s manufacturing jobs are tech-driven, hands-on, and constantly evolving. We’re working with advanced materials, AI, robotics, and even 3D printing. That means every day brings new challenges and opportunities to think critically, solve problems, and make a difference.
The compensation isn’t bad, either. Starting salaries are competitive, and there’s real potential to grow into higher-paying roles. Add in strong benefits and job security, and you’ve got a career that’s both stable and forward-looking.
How can manufacturers meet the needs of both seasoned professionals and next-gen talent?
Having been in the industry this long, I’ve mentored dozens of young professionals, and I’ve learned just as much from them as they have from me. The best companies are the ones that foster cross-generational learning and invest in both new and seasoned workers.
That means offering training for older employees to keep up with new technology, and giving young workers the tools and support they need to thrive. Creating that balance is what keeps teams strong, innovation flowing, and morale high.
Where will manufacturing be 10 years from now?
After four decades in the composites manufacturing industry, I’ve seen a lot change, and all for the better. What was once seen as a rigid, traditional field has evolved into a fast-paced, high-tech, and rewarding career space that I’m proud to be part of.
In the next 10 years, I expect manufacturing to become even more digital, connected, and sustainable. We’ll continue integrating AI, automation, and smart technologies into everything we do. The demand for workers who are tech-savvy, adaptable, and innovative will only grow.
I’ve enjoyed my career so far, but I can confidently say this: There’s never been a more exciting time to be in manufacturing. If you’re looking for a career that challenges you, supports your growth, and makes an impact, this is it.
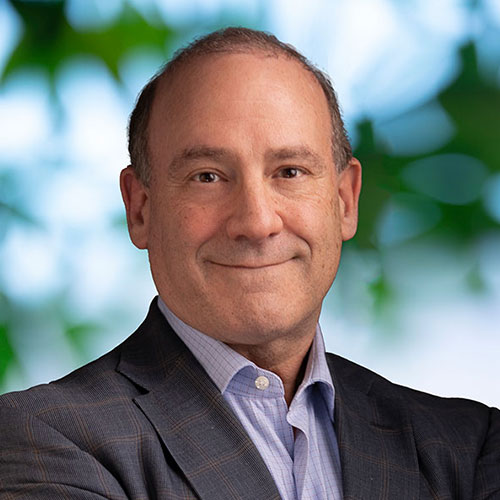
Stephen Gold
President and CEO, Manufacturers Alliance
What can young people expect in terms of professional growth when they pursue a career in manufacturing?
As the manufacturing sector becomes more technologically sophisticated, new roles and specializations are appearing, and the opportunities for professional growth through training and development in multiple fields are emerging proportionate to the dramatic changes occurring in this sector. Indeed, the need for skilled employees in a constantly evolving landscape assures that manufacturing companies are hyper-focused on the continuous professional growth of their workforces. For those entering today’s manufacturing workforce, the sky is the limit.
What are some of the key reasons someone should consider a career in manufacturing?
While career specialists often (correctly) point to manufacturing’s competitive edge in terms of wages and benefits, we know that younger generations are looking beyond a paycheck for something more purposeful. Manufacturing careers can readily serve that purpose. First, manufacturers take pride in making things that people want and need. Every beam in a house, every part in a car, every item in a supermarket was made by a manufacturer. Second, the occupational options are almost limitless. From finance to logistics to IT, HR, marketing, and sales to manufacturing operations, the typical manufacturing company offers a myriad of choices to create a memorable career.
How can manufacturers meet the needs of both seasoned professionals and next-gen talent?
The demographer Neil Howe once stated that for the first time in history, due to the rapid technological changes in society, older generations are learning from — and even deferring to — younger generations. This has altered the historical relationship between generations and offers manufacturers an opportunity to create beneficial synergies among older and younger employees. Thus, while seasoned professionals understand and can mentor processes and culture, next-gen talent comes to the table with unparalleled technical skills to offer their senior colleagues. We see an increasing number of manufacturing leaders meeting the growth needs of both generations by creating win-win circumstances, where intergenerational collaboration leads to the kind of occupational success that everyone yearns for.
Where will manufacturing be 10 years from now?
While manufacturing has seen much transformation over the centuries, the most recent — those changes at the core of the Industry 4.0 revolution — when combined with the complexities of a global value chain, represent the most dramatic ever witnessed. A decade hence, the level of technological sophistication and digital interconnectivity along the entire manufacturing value chain will be universal across the sector.
Shop floors and supply chains will integrate humans working with AI in a completely digitalized environment of cyber-physical systems, creating a level of productivity and quality of products never before seen.
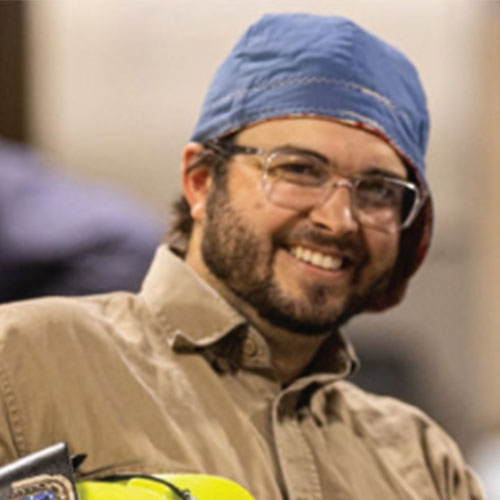
Joe Young
Associate Director, AWS Foundation
What can young people expect in terms of professional growth when they pursue a career in manufacturing?
There’s a huge need for young people in the skilled trades right now. Getting a job in manufacturing isn’t a dead-end; it’s a launchpad. Welding is one of the few careers where you can start with a torch in hand and end up in an engineering lab or running your own inspection business. In fact, WeldingWorkforceData.com estimates we’ll need more than 320,000 welding professionals by 2029. That demand creates opportunities to grow, whether it’s moving into robotics and automation, taking on supervisory roles, or diving into research and development. There’s no single path, and that’s part of what makes it such a strong career choice.
What are some of the key reasons someone should consider a career in manufacturing?
Welding touches almost everything we rely on — appliances, vehicles, medical equipment, buildings, bridges, and much more. It’s behind the scenes of daily life. People in the skilled trades don’t just make things; they solve problems, build critical infrastructure, and keep industries moving. Manufacturing careers, especially in welding, attract people who are driven to grow and take pride in their work. Plus, since it doesn’t require a four-year degree to get started, it’s a smart path for anyone ready to learn and start earning a solid income quickly.
How can manufacturers meet the needs of both seasoned professionals and next-gen talent?
It is imperative that the transfer of institutional knowledge is passed from generation to generation. Mentorships and apprenticeship programs are a proven way to bridge that gap, giving experienced welders the opportunity to pass on what they’ve learned while helping new talent build real-world skills. At the same time, welding is evolving. Advancements in automation, robotics, and digital controls are changing how work gets done. For younger professionals, especially those who’ve grown up with technology, these tools show that welding isn’t stuck in the past; it’s a hands-on career with high-tech possibilities.
Where will manufacturing be 10 years from now?
Ten years from now, manufacturing will be faster, smarter, and more connected, but it will still need skilled people at the core. Welding will continue to evolve with automation, AI, and advanced materials, but the industry won’t run on technology alone. The welders of tomorrow will need both hands-on skills and digital fluency — people who can run a torch and program a robot.