An award-winning engineering and manufacturing firm is recruiting and training tomorrow’s employees today.
A trained, reliable workforce is the most vital resource of any industry. In the manufacturing sector, that resource is in crisis; by 2030 it’s predicted that the industry will be unable to fill up to 2.1 million jobs. Reversing this trend requires cultivating tomorrow’s workers today.
Wade Larson, director of Workforce Development at Wagstaff Inc., a leading aluminum casting equipment manufacturer in Spokane Valley, Washington, understands this. “Our goal is to increase exposure to careers in the trades,” he said. “Get that exposure to kids at younger ages and provide hands-on opportunities to ‘experience’ these careers, rather than just talking about them.”
Bridging the gap
The key is to make students and their families aware of alternatives to the traditional four-year degree track. Although confidence in the traditional college degree has fallen in recent years, it’s still a “default” option for many high school graduates seeking a stable and rewarding career. The key is to educate young students about the possibilities of manufacturing careers while they’re still in school.
That’s just half of the solution, however. Making young people aware of the potential in manufacturing careers won’t magically transform them into skilled, knowledgeable workers who can simply step into the roles of retiring staff. Companies that want to survive the skilled worker crisis will need to help students graduate high school with the credentials necessary for trades like welding or machining, and be willing to invest in their future workforce.
Creating a model
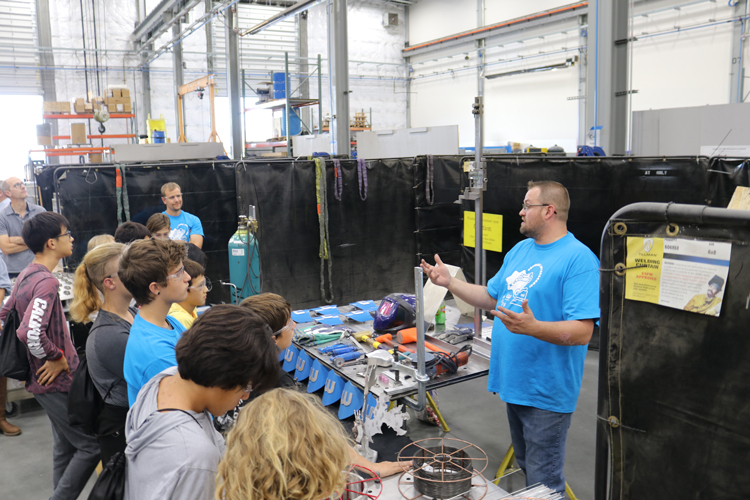
Wagstaff has taken a leading role in investing in its present and upcoming workforce, and the local community has been impressed: The company was awarded 2023 Manufacturer of the Year by the Association of Washington Business.
One reason for Wagstaff’s success is its support for its employees both current and future. One way they do this is by acting as a “workforce development institution,” setting up internal programs utilizing competency-based learning to train and upskill their employees and remain inspired.
It also means being a model for other companies seeking to recruit the next generation of skilled workers. Wagstaff has helped develop several programs designed to help young people see the trades and manufacturing jobs as the great careers they are. For example, the company sponsors a Business After School Program focused on manufacturing, creating a hands-on, immersive encounter that allows students to experience a manufacturing career firsthand. The company also partnered with a local school district to successfully land a $200,000 grant for a student-led renovation and modernization of the school’s wood and metal shop facilities, as well as providing employee mentors to help the students through the process.
The backbone
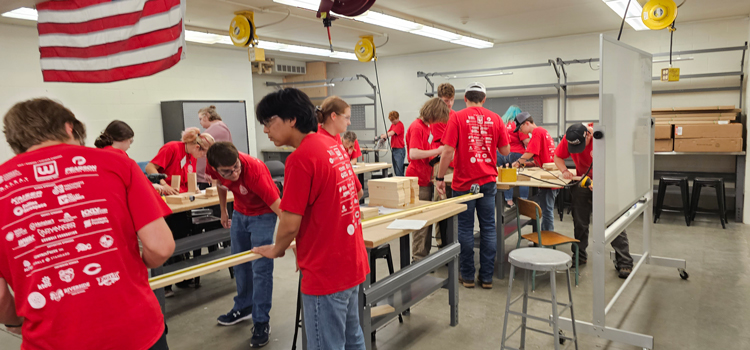
One of Wagstaff’s most successful projects has been the Production and Manufacturing Institute. Launched in 2019, this is a three-week program where students form teams that design, build, and sell a product in a real production environment, learning every aspect of the manufacturing process along the way.
“Our summer Institute is meant to be the ‘backbone’ to creating a manufacturing network in the area,” Larson noted. “And it has done well. We grew to four locations in 2023, and we expect to launch eight to ten locations in 2024.”
All of the company’s initiatives share the dual purpose of enriching the community and exposing students to the huge opportunities presented by a career in manufacturing. “Here at Wagstaff,” Larson said, “we are committed to promoting multiple career pathways to students beyond the four-year degree track, and developing a qualified workforce ready to go to work right out of high school.”
To learn more, visit Wagstaff.com